The production of a toilet begins with the casting of its core components. High-quality ceramic clay is mixed with water and other additives to achieve the desired consistency. This mixture is then poured into molds, where it is shaped into the various parts of the toilet, such as the bowl, tank, and lid. The casted parts are left to dry and harden, a process that can take several days. Once dry, they are fired in a kiln at temperatures exceeding 1200 degrees Celsius, which vitrifies the clay and gives the ceramic its durability and smooth surface.
After the firing process, the ceramic parts are inspected for any defects and then glazed. The glaze is a layer of liquid glass that is applied to the surface of the components to provide a water-resistant and easy-to-clean finish. The glazed parts are then fired again at a slightly lower temperature to bond the glaze to the ceramic. Once the glazing is complete, the individual parts are assembled. The bowl and tank are joined together, and the flushing mechanism, including the float arm and valve, is installed. The toilet is then fitted with the necessary hardware, such as bolts and nuts, to secure it to the floor and connect it to the water supply. Finally, the toilet is inspected and tested to ensure it meets quality standards before being packaged and shipped.
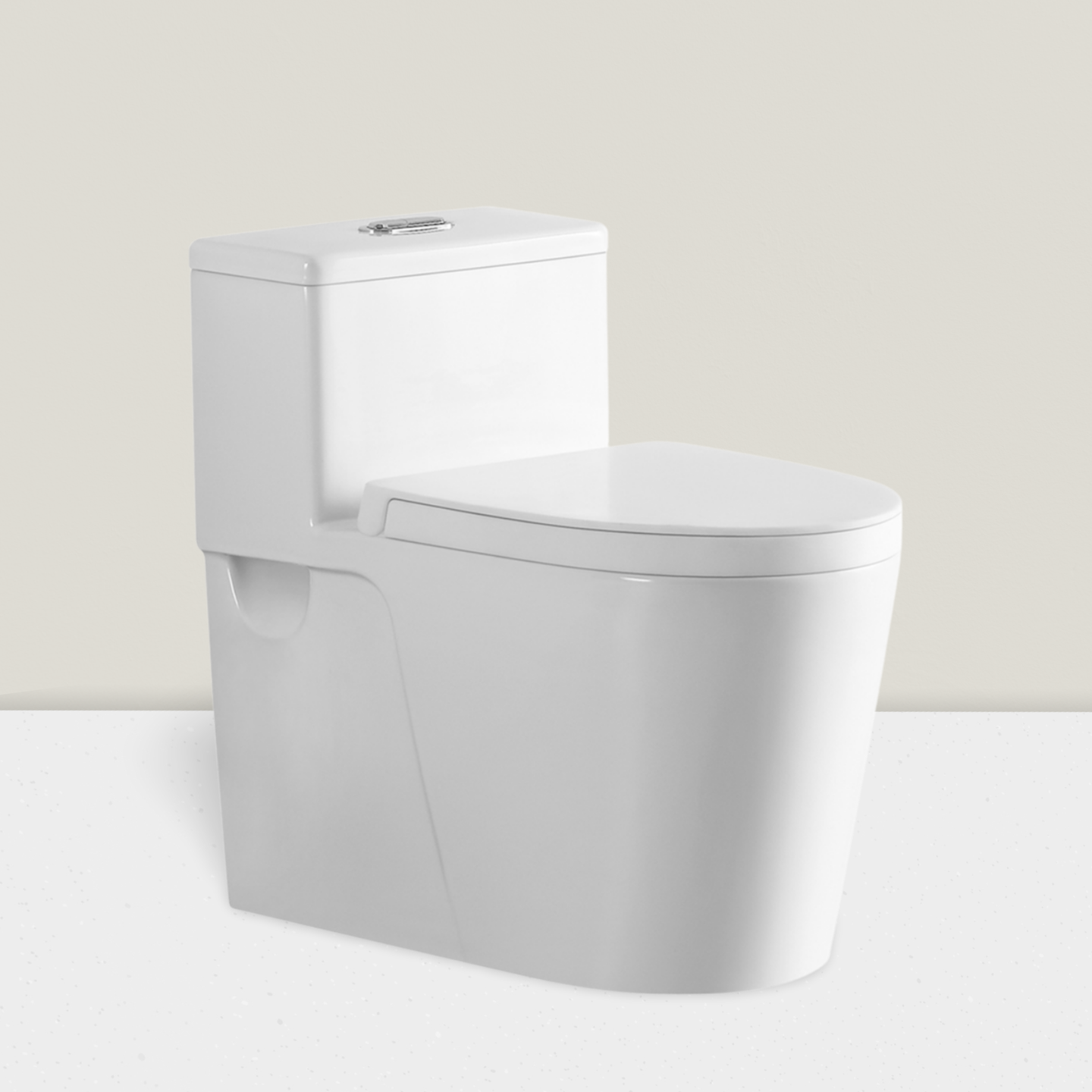